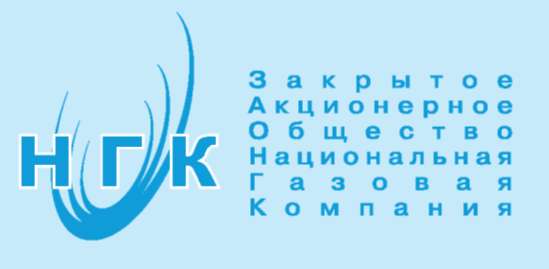
Разработка инновационных технологий в области физико-химических процессов с их последующим внедрением в различных отраслях промышленности
Увеличение эффективности нефтедобычи за счет использования малогабаритной универсальной установки по переработке попутного нефтяного газа и газового конденсата с получением фракций растворителя и дизельного топлива
Разработчик — ЗАО «Национальная газовая компания»
Введение
Для поддержания и увеличения нефтеотдачи применяются разнообразные растворители асфальтеновых и парафиновых отложений (АСПО). Стоимость промышленно выпускаемых растворителей этого класса (Нефрас, ПАЛР и др.) достигает 20 тыс. руб. за тонну. Применение их сопряжено с необходимостью комплексного решения вопросов завоза, складирования и другими мероприятиями, увеличивающими эксплуатационные издержки, приводящими к снижению эффективности использования данного метода химического воздействия на нефтеотдачу.
Известными факторами, снижающими общую эффективность добычи углеводородного сырья месторождений, являются отсутствие технологий использования попутного нефтяного газа (ПНГ) непосредственно на месторождениях. Большим резервом является наличие вблизи действующих нефтепромысловых участков запасов газоконденсатов, однако значительная стоимость транспортировки сопутствующих газоконденсатных ресурсов и отсутствие эффективных методов переработки их на местах не позволяет использовать данный ресурс.
Существенным фактором увеличения эффективности нефтедобычи является повышение качества (сортности) нефти непосредственно на промысловых участках. Этого можно достигнуть с помощью технологии получения водорода из природного или попутного газа и установки аппарата гидроочистки нефти. Образующиеся при этом отходы в виде сажи и смолистых углеводородных соединений можно перерабатывать в брикетированные продукты с транспортировкой и реализацией как топливное сырье и сырье для нефтехимической, строительной и других отраслей промышленности.
Наш проект предусматривает поэтапное увеличение эффективности нефтедобычи за счет реализации на месторождении комплекса технологий с постепенным наращиванием набора оборудования. На каждом этапе новые технологические единицы дополняют предыдущие с возможностью расширения на основе модульного принципа. Основные этапы реализации предусматривают следующие технологические ступени:
— создание на базе минимального набора оборудования модульной установки производства растворителей АСПО, а также производства сжиженного газа и газового бензина за счет использования ПНГ 3-й ступени сепарации и частично 2-й ступени сепарации;
— расширение спектра производимых на месторождении растворителей и выпуск товарных сортов моторных топлив и сжиженных газов за счет использования газоконден-сатных ресурсов;
— дооборудование комплекса блоками пиролиза газа, газоразделения с получением водорода, гидроочистки нефти и утилизации отходов переработки газа.
Основными технологическими достижениями нашей компании, применимыми для создания перечисленных комплексов, являются разрабатываемые и внедряемые в существующие производства следующие аппараты и процессы:
— газо-жидкостные эжекторы с профилированной сверхзвуковой частью для увеличения давления газовых потоков без применения компрессоров, использованы на НПУ-100 ОАО «Таас-Юрях нефть» (Якутия) в 1999—2002 гг., испытаны на Кирово-Чепец-ком химкомбинате для отработки технологии получения продуктов хлорирования природного газа в 2008 г.;
— малозатратный процесс выделения фракций растворителя, примененный в нашем проекте модернизации НПУ-100 ОАО «Тульская топливно-энергетическая компания» и реализуемый в настоящее время;
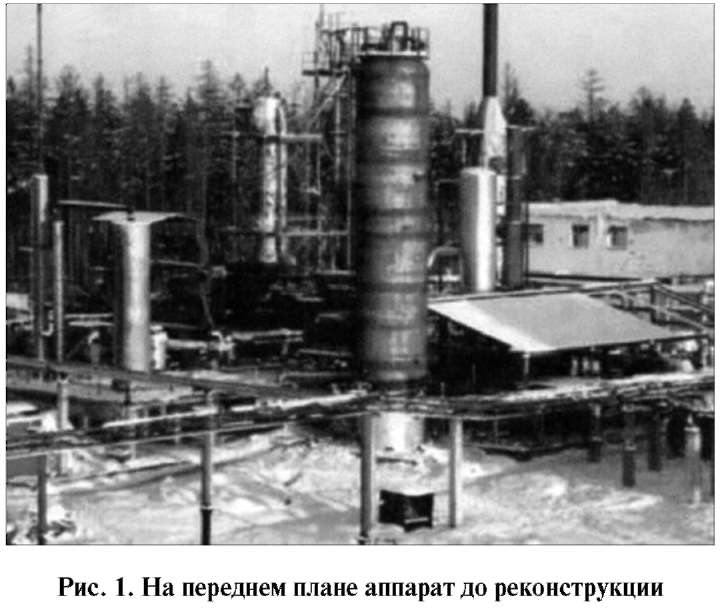
— приспособление типовых емкостных аппаратов. Так, например, была разработана конструкция, в которой корпус реактора термического крекинга (рис. 1) был переоборудован под ректификационный аппарат канального типа с объединением в одном аппарате функций нескольких колонн. Успешная эксплуатация переоборудованного аппарата была произведена на НПУ-100 ОАО «Таас-Юрях нефть». Производительность установки была увеличена со 100 до 150 тыс. тонн в год. При этом штатные колонные аппараты (на заднем плане) были задействованы на вторичном процессе — термическом риформинге прямогон-ной бензиновой фракции, а также для малотоннажной переработки газового конденсата;
— технология термической конверсии метана, предложенная нашей компанией и защищенная рядом российских и международных патентов, позволяющая реализовать одностадийный процесс превращения метана (а также и других углеводородов) в этилен и водородсодержащий газ с последующей каталитической переработкой этилена и других непредельных углеводородов в товарные продукты на основе известных технологий (процессы МТО, МТР, фирмы UOP, Lurgi);
— высокоинтенсивные массообменные пенные аппараты, внедренные нашей компанией в 2005—2009 гг. в ряде технологических процессов на заводах по производству удобрений, гранулированных продуктов и в других производствах (Кирово-Чепецк, Березники).
Также использован опыт газоразделения попутного нефтяного газа (ПНГ) с получением широкой фракции легких углеводородов (ШФЛУ) и стабильного газового бензина (СГБ) при отсутствии приемной и дожимной компрессорных станций и холодильных установок (ПХУ — на пропановом или аналогичном цикле), что также требует применения мощных компрессорных установок. Авторами проекта проведена серия разработок для газоперерабатывающих предприятий АК «СИБУР» в 2002—2004 гг. в период, когда несколько заводов этой компании не обеспечивались оборудованием для полного цикла газопереработки. За этот период разработаны и внедрены схемы без использования ПХУ, а также схемы с повышением выхода ШФЛУ за счет использования нестандартного холо-дообразующего и сепарационного оборудования. Такие схемы были внедрены на Южно-Балыкском, Муравленковском, Красноленинском и других заводах.
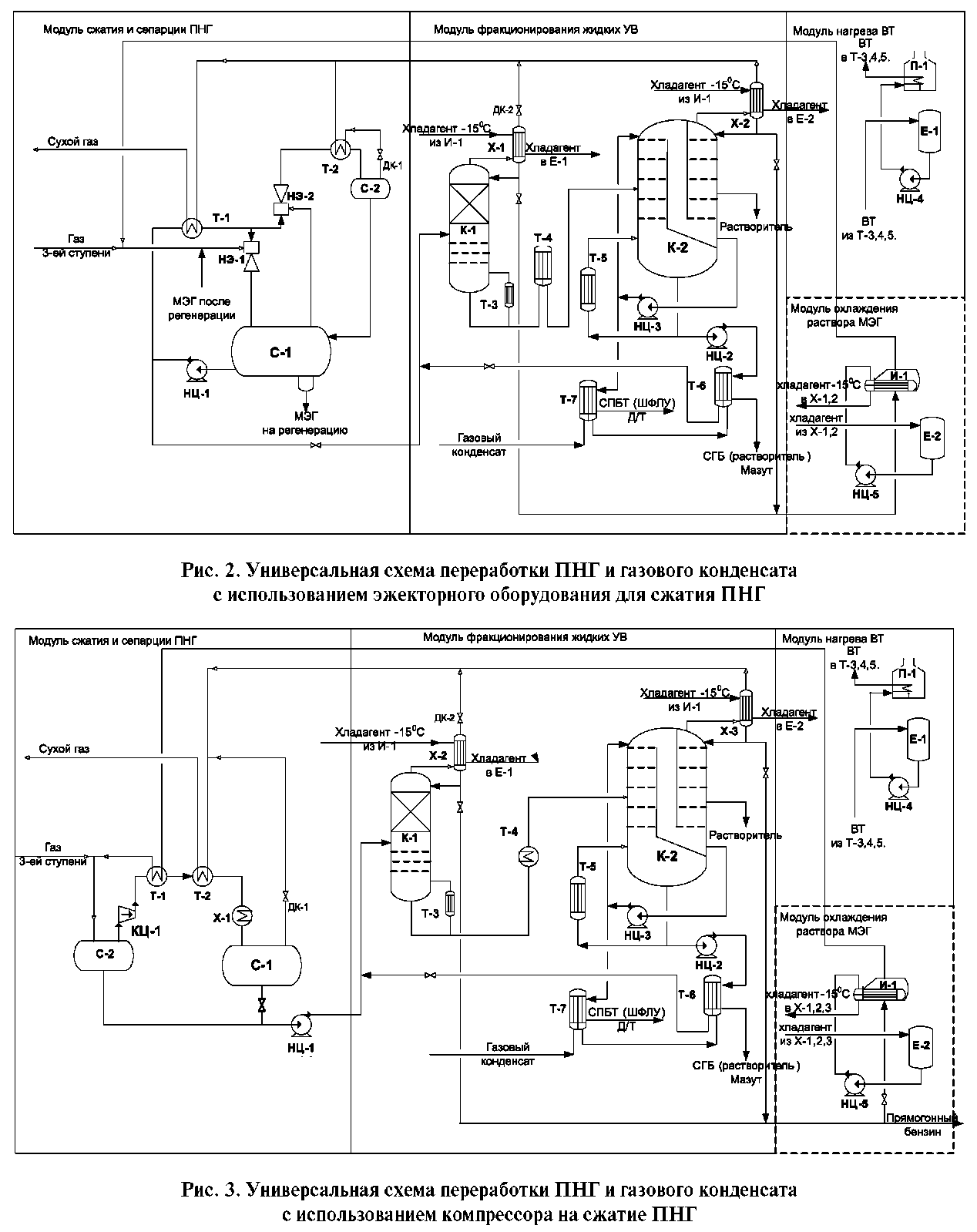
Назначение
На первых этапах реализуется проект малогабаритной модульной установки, предназначенной для получения из углеводородного сырья широкого ассортимента различных фракций: СПБТ (ШФЛУ), СГБ (растворителя), прямогонного бензина, дизельного топлива, растворителя парафиноотложений, дизельного топлива в удаленных регионах или малодебитных месторождений нефтегазодобывающих предприятий. Варианты принципиальной технологической схемы представлены на рис. 2, 3.
Технические характеристики
Установка состоит из транспортабельных модулей:
— модуль сжатия и низкотемпературной сепарации;
— модуль ректификационного фракционирования жидких углеводородов;
— печной модуль нагрева циркулирующего высокотемпературного теплоносителя (ВТ);
— модуль охлаждения циркулирующего рассола.
Первый модуль может быть использован на первом этапе как самостоятельная установка получения гексан-октановой фракции растворителя АСПО и сжиженного газа.
В установке фракционирования сжиженных углевородов ПНГ или газового конденсата использован процесс ректификации, реализованный в колонном аппарате канального исполнения.
Схемы соединений оборудования, автоматизации и управления аналогичны схемам газофракционирования и ректификационного погоноразделения.
Размещение оборудования модулей предусмотрено преимущественно в утеплённых боксах на рамном основании.
Преимущества установки
Отличительной особенностью представленной схемы установки является возможность переработки, как газового конденсата, так и попутного нефтяного газа с получением широкого спектра продуктов. Реализация процесса ректификации в колонном аппарате канального типа позволяет обеспечить высокую степень погоноразделения и уменьшить габариты фракционирующего оборудования, что снижает металлоемкость по сравнению с ректификацией в аппаратах вертикального исполнения. Снижение металлоемкости оборудования позволяет обходиться без массивных опорных фундаментов и упрощает перевоз и монтаж оборудования. Существенно снижается также ветровая нагрузка на аппарат.
При отсутствии компрессорной станции возможно увеличение давления поступающего газа при использовании двухфазного эжектора. Основным энергопотребляющим агрегатом при этом является насос для жидкой фазы углеводородов — на рисунке представлена схема с использованием струйных аппаратов. Давление ПНГ в схеме с двухфазным эжектором увеличивается, что позволяет использовать дроссель в качестве холодообразующего элемента.
Возможны варианты с использованием небольшого (одноступенчатого) компрессора и одно- или двухступенчатого эжектора. При наличии холодообразующих дросселирующих элементов и циркулирующей пропановой фракции получение сжиженных газов и растворителя производится без применения дорогостоящей автономной пропановой холодильной установки. В качестве холодообразующего устройства возможно также применение достаточно простых и проверенных в эксплуатации сверхзвуковых конден-сатовыделяющих устройств SST (фирма «ЭНГО»), вихревых трубок Ранка-Хилша или турбодетандеров. Последние имеют высокий коэффициент получения холода, но являются дорогостоящими элементами.
Указанные особенности разработанного процесса способствуют эффективному его использованию в малотоннажной технологии.
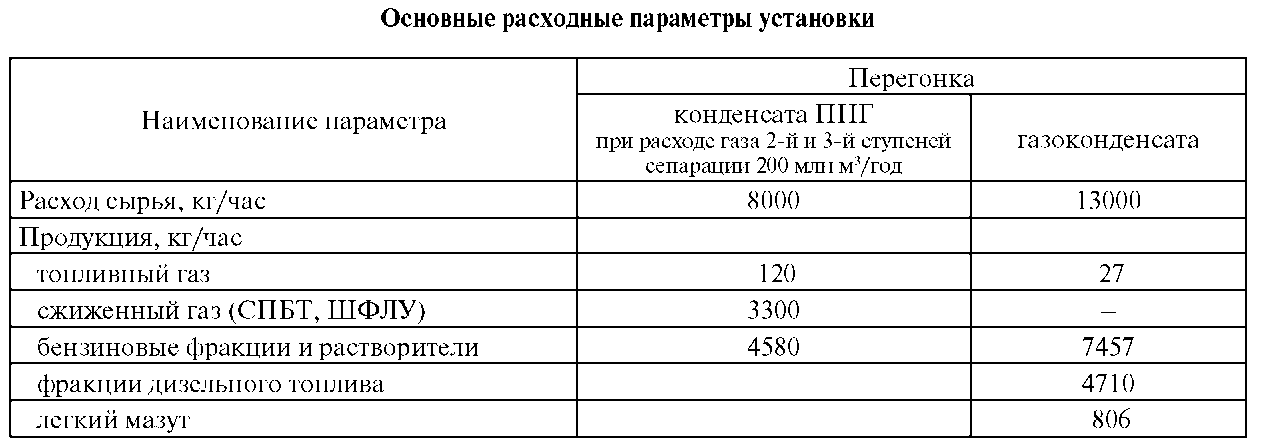
Уменьшение стоимости сырьевой компоненты в производстве этилена
ИСХОДНОЕ СЫРЬЁ
Основным сырьем для пиролиза с целью получения этилена в трубчатых печах являются на сегодняшний день этан, пропан и бутан, содержащиеся в попутных газах нефтедобычи и в нефтезаводских газах, газовые бензины, газаконденсатные бензины, бензины прямой гонки нефти, а также рафинаты каталитического риформинга, после удаления из них ароматических углеводородов. Газообразное сырьё является наилучшим сырьём с точки зрения получения максимальных выходов этилена и пропилена. Состав продуктов пиролиза этого сырья зависит от глубины конверсии (степени превращения). На практике степень превращения сырья может колебаться в широких пределах, так в промышленных условиях степень превращения пропана достигает 85-90% за проход. С увеличением степени превращения пропана селективность падает, так как выход побочных продуктов растет быстрее, чем выход этилена. Следовательно, требуется больше сырья, чтобы обеспечить нужный выход этилена. Это приводит к увеличению нагрузок на узлы комприми-рования и системы газоразделения, а значит и к увеличению энергетических затрат.
Известен инициирующий эффект добавки легких углеводородов к более тяжелым углеводородам, причем распад легких углеводородов ускоряется, а более тяжелых остается прежним или немного замедляется при одинаковых их исходных мольных концентрациях в сырьевой смеси. В качестве легких углеводородов предлагается использовать Н2, СН4 или С2Н6.
В настоящее время с целью улучшения технико-экономических показателей процесса на пиролиз возвращают этановую (пропановую) фракцию и а также другие потоки (рецикл). Выход этилена при совместном пиролизе легкого и более тяжелого газообразного сырья выше, чем при раздельном только при соотношениях легкий углеводород : тяжелый углеводород не менее, чем 1,0-1,2 : 1,0 (в сторону увеличения количества легкого сырья в смеси). Также легкие добавки и использование рецикла некалькулируемых алкановых потоков процесса позволяют при совместном пиролизе увеличить выход именно этилена и снизить выход пропилена. При добавке к пропану этана возрастает выход метана, тогда как метановая добавка к пропану снижает степень образования метана из пропана. Наиболее изучены сырьевые смеси этан-пропан, а также метан-этан-пропан. (Fromert G.F, Van de Steene B.O., Sumedha O.//Oil a. Gas J.1979.V.77. № 16.P.87-90; Ross L., Shu W.R.// Oil a. Gas J.1977.V.73. № 43.P.58-64)
Таким образом, наиболее перспективный вариант — это использование смесевого сырья и рециклов полупродуктов и побочных продуктов пиролиза с целью увеличения степени конверсии в процессе снижения производительности установки по исходному покупному сырью.
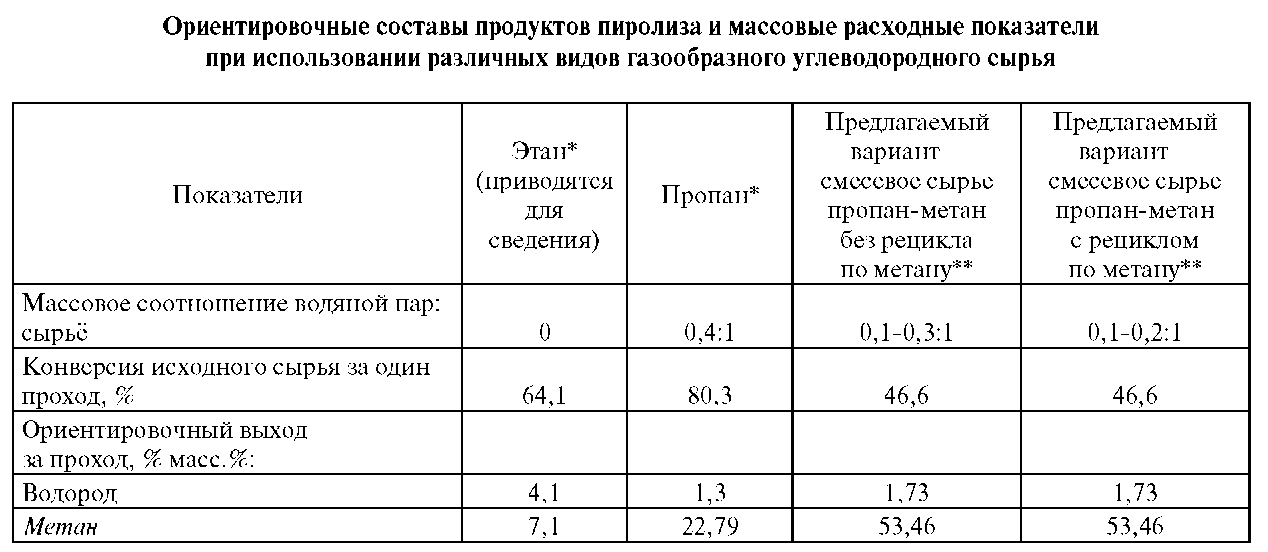
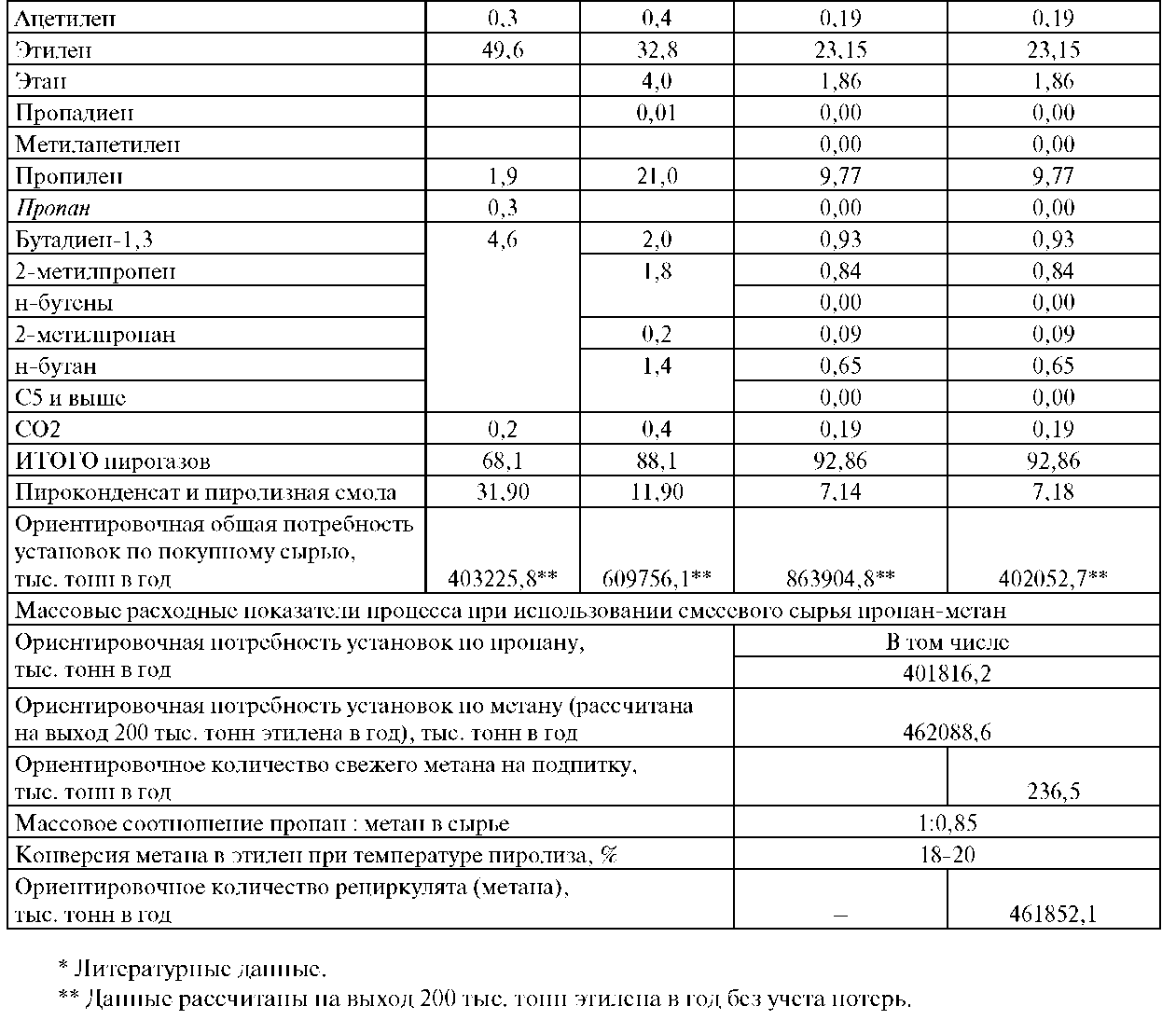
Таким образом, наиболее выгодным с технологической стороны может быть предлагаемый вариант работы установки на сырье — смесь пропана с метаном с рециклом по метану. Это позволит получить требуемый выход целевого продукта — этилена 200,0 тыс. тонн в год, причем со значительным снижением расхода потребляемого установкой покупного сырья. При этом массовый расход сырьевого пропана снизится более чем в два раза, тогда как все остальные параметры типового процесса пиролиза будут сохраняться. С другой стороны, в процессе может быть достигнута достаточная степень превращения сырья в целевой компонент — этилен и высокая селективность процесса по этилену. Это в свою очередь приведет к уменьшению общего расхода покупного сырья почти на 462,0,0 тыс. тонн в год, а рециркуляция метановой фракции будет значительно повышать степень использования собственных ресурсов установки за счет получения из этой фракции дополнительного количества целевого продукта — этилена.
ЗАО «Национальная Газовая Компания»
117105, г. Москва, ул Нагатинская, д.1, стр. 2
Тел.: (495) 7815472; (495) 7815470; www.gazcompany.ru